
“Baader offers integrated anatomical wing segmenting and whole wing cutting which is an essential step for automatic breast deboning,” he said. However, most processors are not willing to sacrifice final product quality and yield in exchange for automation. Oliver Hahn, chief executive officer of Kansas City, Kan.-based Baader Poultry USA, said integrated anatomical wing segmenting and whole wing cutting are essential steps for automatic breast deboning.
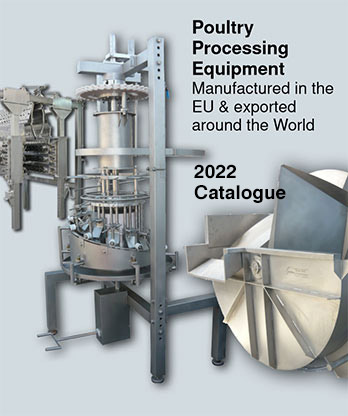
A combination of the unique ACM-NT shackle and turning mechanisms within the system allows products to be held and positioned perfectly for each cutting operation, resulting in optimum yield as well as top presentation and quality.” “Systems can be configured to suit the exact processing and layout requirements of each individual plant. “Flexible, modular and precise, ACM-NT uses the unique Sigma overhead conveyor its layout is infinitely flexible,” said Roy Driessen, industry marketing manager of poultry at Marel, with US operations in Lenexa, Kan.

Driessen noted the ACM-NT system will handle both air and water chilled products. Marel Poultry offers processors an automatic modular in-line cut-up system capable of handling up to 6,500 broilers per hour. “Safety for personnel working with these pieces of equipment is always under consideration, and we keep updating our equipment to be seen as the safest equipment in the market.” “Human interaction remains an important part of automation,” Nolten said. “Based on these data parameters, broilers, legs and wings can pass through a cut-up machine or bypass it.”Īnother trend is the increased weight range a cut-up machine can process in one setting so there are fewer setting adjustments needed during processing. “I think the most notable trends are the increased use of smart data (matching the flock characteristics with the desired output based on parameters like weight or quality) to channel each broiler to the most ideal cut,” he said. However, that is much faster than the legally allowed speed in the United States.Įric Nolten, vice president of commercial operations for Meyn America, Ball Ground, Ga., noted cut-up lines are operating at speeds of 7,500 bph, so, the ideal set-up is a dual cut-up and deboning line per single slaughtering and evisceration line. Globally, poultry processing line speeds are slowly progressing to 15,000 birds per hour (bph). Automatic cut-up lines decrease manual labor. The current pandemic showed how vulnerable workers in processing plants can be.
